在航空航天、汽车电子、新能源等高级制造领域,产品需经受异常温度、湿度及快速温变的严苛考验。
高低温冲击湿热试验箱作为环境适应性测试的核心设备,通过模拟“冰火两重天”与湿热交变的异常条件,精准评估材料与产品的可靠性,成为缩短研发周期、降低质量风险的关键工具。
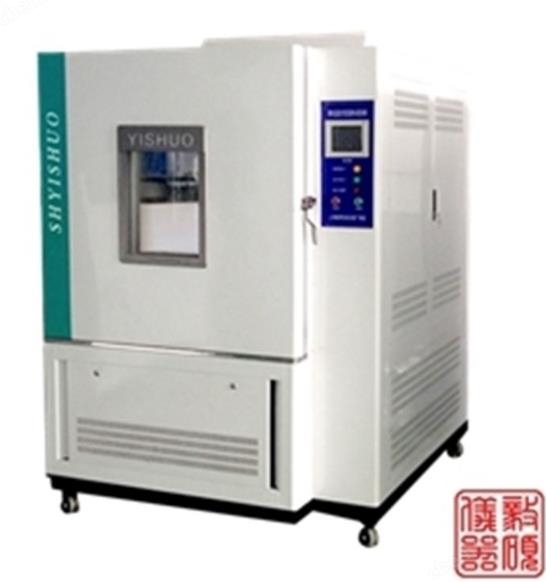
一、温度冲击:异常温差下的性能突围
高低温冲击湿热试验箱采用独立高温区(通常达150-200℃)与低温区(-70℃至0℃),通过移动试样或快速切换气流,实现每分钟30℃以上的温变速率。例如,某新能源汽车电池包需在-40℃至85℃间循环冲击,模拟极寒启动与高温快充场景。试验箱通过风冷/液氮双模式制冷系统,确保低温区快速降温至-70℃,同时高温区采用PID控温技术维持±0.5℃精度。某品牌试验箱实测数据显示,其可在10秒内完成-40℃至125℃的切换,精准复现产品在实际使用中因环境突变导致的热应力冲击。
二、湿热交变:腐蚀与绝缘的双重挑战
湿热试验模块通过精确控制温度(20-95℃)与湿度(20%-98%RH),模拟沿海、雨季等高湿环境。在电子元器件测试中,湿热环境会加速金属氧化、绝缘材料吸湿,导致接触电阻升高或短路。试验箱采用超声波加湿与除湿系统,配合316L不锈钢内胆,确保湿度均匀性±2%RH。例如,某通信设备制造商利用该设备发现,其5G基站模块在85℃/85%RH条件下持续暴露72小时后,PCB板出现铜箔剥离,据此优化了三防涂层工艺,使产品湿热寿命提升3倍。
三、综合测试:多环境耦合的可靠性验证
高级试验箱集成温度冲击与湿热循环功能,形成“高温高湿→低温→湿热→高温”的复合测试流程。某航空电子设备需通过GJB 150A标准中的“温度-湿度-振动”三综合试验,试验箱通过与振动台联动,在-55℃至125℃、95%RH环境下施加随机振动,精准定位焊点疲劳、封装开裂等失效模式。数据显示,经此类综合测试的产品,现场故障率较传统测试降低67%,研发返工成本减少42%。
从材料筛选到成品认证,高低温冲击湿热试验箱通过模拟真实世界的异常环境,为产品可靠性提供了量化依据。随着工业4.0与AI技术的融合,试验箱正朝着智能化(自动生成测试报告)、模块化(支持定制化环境组合)方向发展,持续赋能高级制造的品质升级。